What is automated machine tending?
Kolektor Digital's KoCo robot, equipped with a Zivid 3D camera, showcased its capabilities in a machine tending demonstration. Learn more.
Machine tending involves loading and unloading parts using industrial or collaborative robots. The choice of a vision system, particularly a 3D camera, is crucial for accurate object detection and precise pick-and-place operations.
A high-resolution Zivid 3D camera improves object recognition, even for shiny or complex parts, enabling precise and demanding pick-and-place tasks in machine tending applications.
3D vision in machine tending
Correct Placement and Orientation
Vision-guided robots perform precise pick-and-place tasks, ensuring accurate placement and orientation while avoiding collisions and potential damage.
Capture Any Material
A 3D vision camera captures highly detailed, accurate, and complete point clouds—even for small, reflective, or complex assembly parts.
Flexible 3D Positioning
Capture objects from multiple angles and viewpoints to eliminate blind spots, reduce occlusion, and minimize point cloud artifacts.
Why use a Zivid camera?
Can you see the difference?
True-to-Reality 3D Vision
Accurate perception of objects and their corresponding assembly points is crucial for reliable machine tending. These tasks often demand alignment at the millimeter level, where even minor deviations can result in mispicks or incorrect placements. Without high-fidelity, true-to-reality 3D vision, consistency and reliability suffer.
Zivid 3D cameras offer best-in-class trueness of over 99.8%, ensuring highly accurate representation of an object’s form, shape, and position. This level of precision allows machine tending robots to detect even small parts and fine details, enabling successful and repeatable handling, alignment, and processing.
Precision on the move
Precision is critical in machine tending tasks as accurate placement depends on accurate picking. Even slight deviations in the pick point can result in misaligned parts, leading to improper machine loading or fitting failures. These errors can be costly, requiring additional equipment, workspace, and time to correct.
Zivid 3D cameras are perfectly suited for robot-mounted applications, enabling the robot’s vision system to move dynamically. This mobility allows the camera to capture the scene from optimal angles and positions, ensuring reliable and precise part localization.
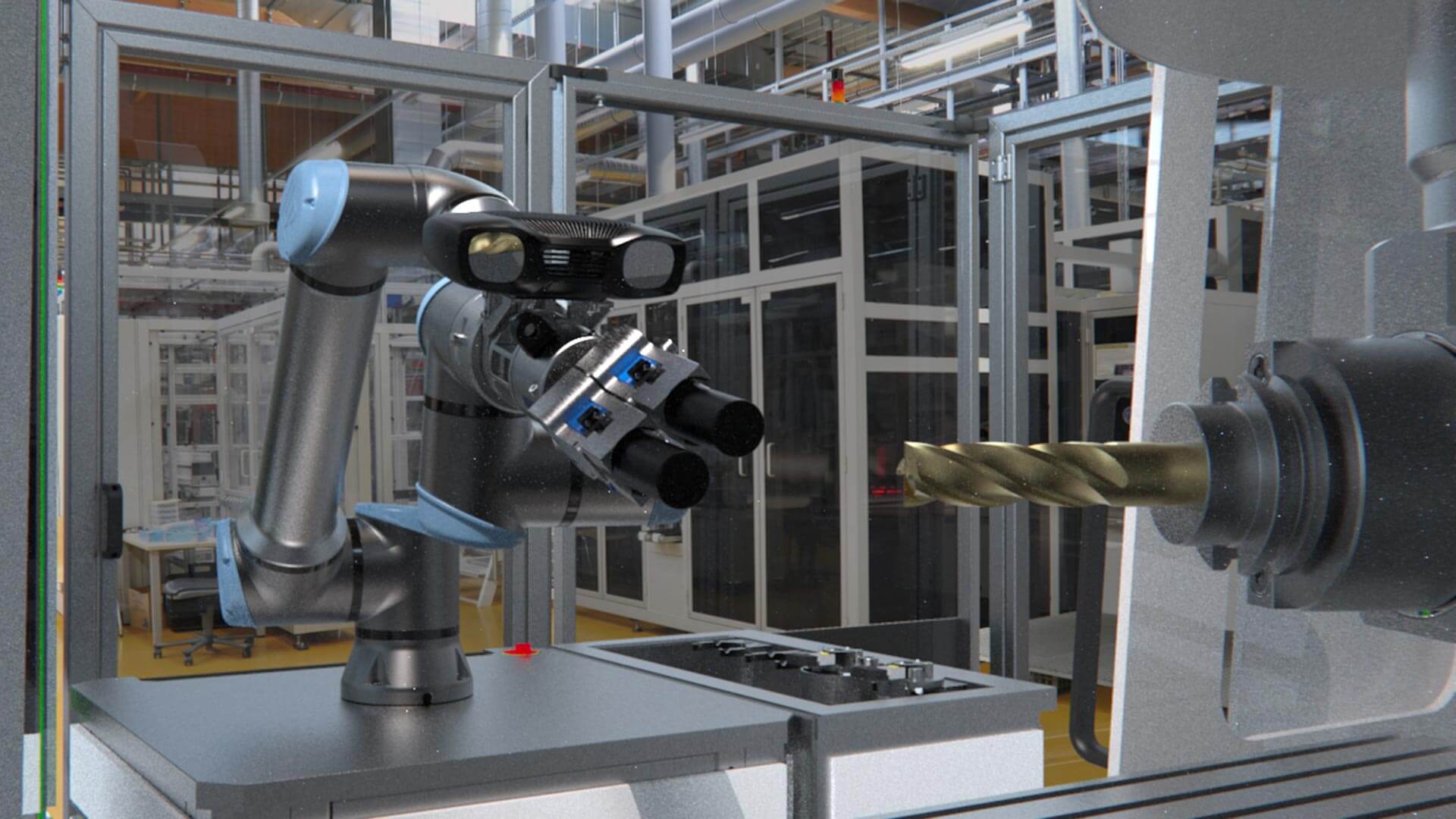
Reliable 3D Vision for Shiny and Metallic Parts
Robotic part picking and manipulation often involves shiny metallic items. It is essential that the vision system can extract complete and accurate data on these parts with a minimum of reflection artifacts.
With the best dynamic range in the industry, and patented imaging tools such as HDR and Sage Engine, Zivid cameras can cope with the most challenging objects found in manufacturing.
Before vs. After applying the Sage Engine
Other 3D vision solutions
❌ The robot has difficulty handling a wide variety of objects, especially small items such as screws.
❌ The vision system struggles to capture complete point clouds on highly reflective or black materials due to imaging artifacts.
❌ The robot cannot clearly identify parts and their boundaries and find the optimal pick point.
❌ The 3D camera is not suitable for robot-mounted use.
❌ Camera lacks true industrial grade robustness and struggles with stability.
With Zivid 3D camera
✅ The robot can capture millimeter level detail with high accuracy.
✅ The vision system can handle a wide variety of challenging items and materials, including shiny metallic parts.
✅ The robot can clearly identify a parts shape and its position to find the ideal pick pose.
✅ Zivid 3D cameras are comfortable and excel when mounted on the robot.
✅ Delivers ultra-stable 3D data with near total immunity to ambient light levels.
Customer Stories
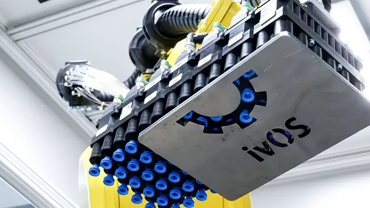
J. Schmalz | Ready to Automate Sheet Metal Handling
Schmalz developed the Solution Kit ivOS Sheet Metal to automate handling of unknown parts.
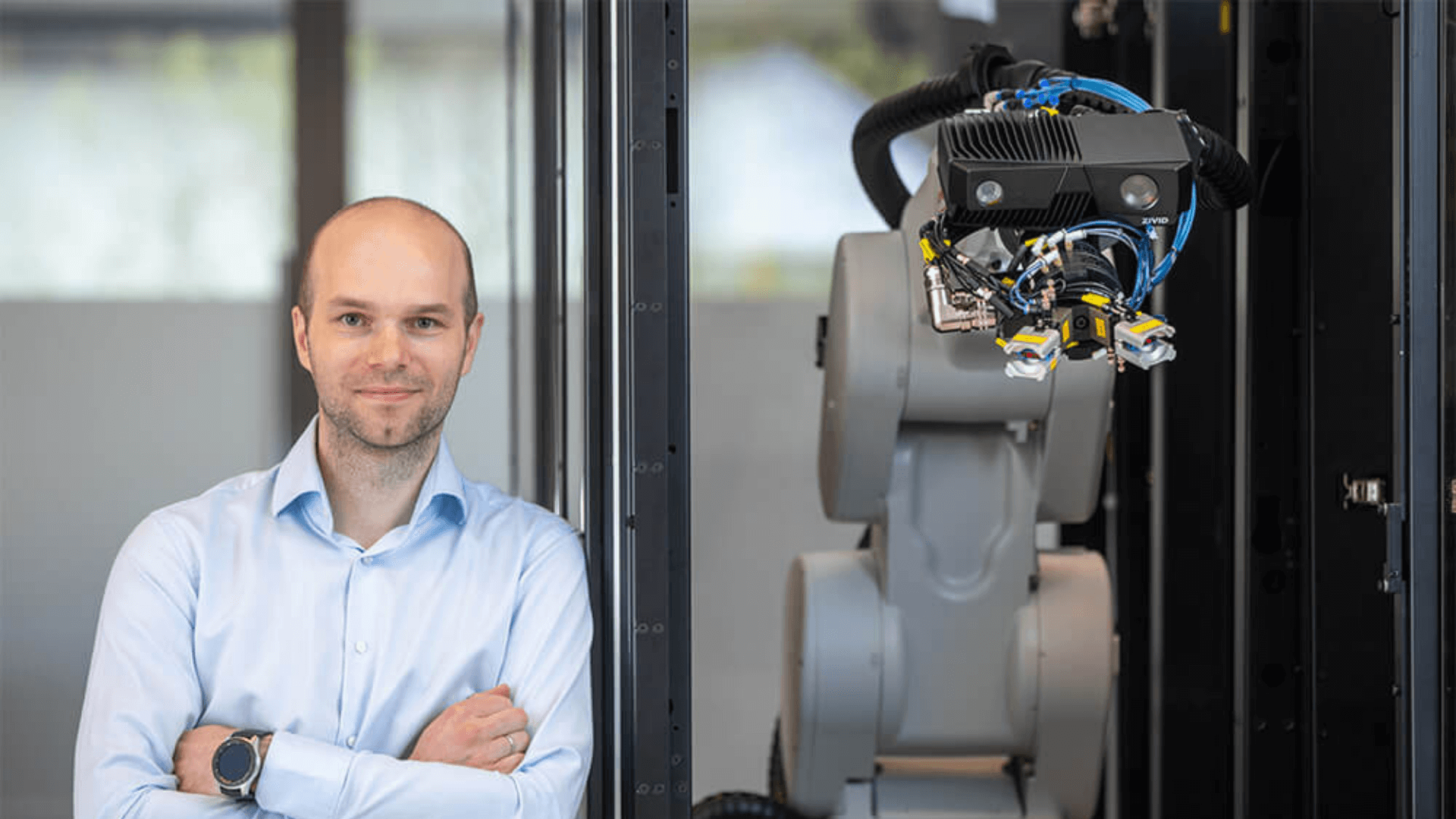
Kolektor | Envisioning robot workers
Kolektor Digital needed a 3D machine vision camera with human-like capability.
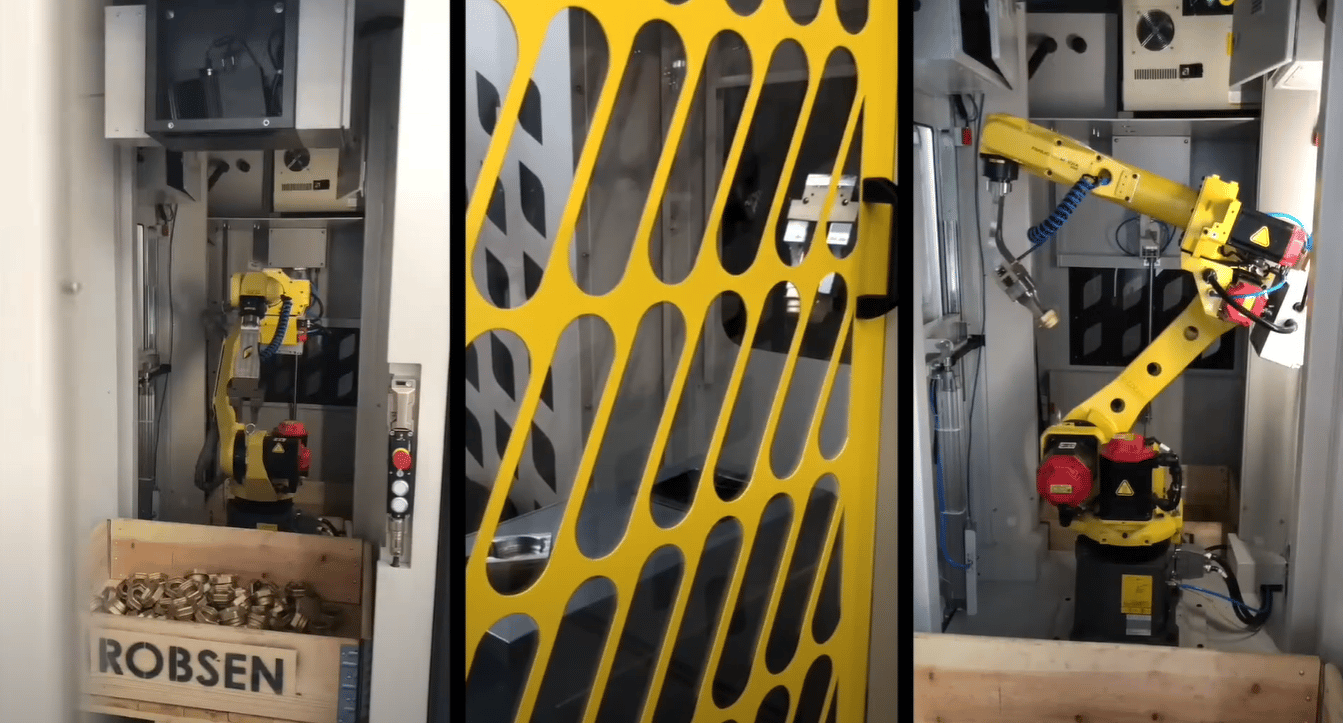