What is bin picking?
Random or automated bin picking is used at the input stage of manufacturing, often in automotive, white goods, or machine tending. A robot empties a bin of bulk parts into a machine, feeder, or conveyor for further processing. Bin-picking usually involves one type of part and requires precise object placement for tasks like stamping or measurement. A suitable 3D vision system is critical, as it affects the robot’s ability to detect, pick, and place parts accurately.
3D vision in bin picking
Improved Object Recognition
With high-resolution, ultra-precise native 3D point clouds, the robot can enhance object recognition and detect a greater number of parts.
Reliable 3D Picking Accuracy
3D vision enables reliable object boundary recognition by accurately capturing object's size, orientation, and absolute position.
Correct Placement and Orientation
Vision-guided robots can perform precise pick-and-place tasks, ensuring accurate placement and orientation while avoiding collisions and damage.
Why use a Zivid camera?
Compare the point cloud quality of Zivid with other widely used 3D camera alternatives in automation - and see why Zivid comes out on top.
Comparison of Zivid (left), a high-end stereo alternative (middle), and a structured light alternative (right) at 350 lux.
Comparison of Zivid (left), a high-end stereo alternative (middle), and a structured light alternative (right) at 1200 lux.
See tiny and detailed objects, densely stacked or randomly arranged
Zivid cameras deliver high-resolution point clouds that are more than 99% true-to-reality in terms of position, dimension and orientation. With a short baseline they minimize occlusion and when mounted on the robot can capture from the optimal position and viewpoint.
- High accuracy for precise pick and place
- Infield correction that allows you to verify dimension trueness of your camera any place, any time
- Hand-eye calibration Zivid handles the math so that our customer just needs to provide the dataset.
Before vs. After applying the Sage Engine
See shiny, reflective, machined, and polished parts
Robotic part picking and manipulation often involves shiny metallic items. It is essential that the vision system can extract complete and accurate data on these parts with a minimum of reflection artifacts.
With the best dynamic range in the industry, and patented imaging tools such as HDR and Sage Engine, Zivid cameras can cope with the most challenging objects found in manufacturing.
Achieve Consistent Results in Real Production Environments
Manufacturing robots depend on 3D vision systems delivering reliable data regardless of environmental conditions.
With a single Zivid camera setting, you can consistently capture robust 2D images and point cloud data, even under changing ambient light conditions. Maintain high picking accuracy despite variations in temperature and lighting intensity.
Other 3D vision solutions
❌ The robot has difficulty handling a wide variety of objects, especially small items such as screws.
❌ The vision system struggles to capture complete point clouds on highly reflective or black materials due to imaging artifacts.
❌ The robot cannot clearly identify parts and their boundaries and find the optimal pick point.
❌ The 3D camera is not suitable for robot-mounted use.
❌ Camera lacks true industrial grade robustness and struggles with stability.
With Zivid 3D camera
✅ The robot can capture millimeter level detail with high accuracy.
✅ The vision system can handle a wide variety of challenging items and materials, including shiny metallic parts.
✅ The robot can clearly identify a parts shape and its position to find the ideal pick pose.
✅ Zivid 3D cameras are comfortable and excel when mounted on the robot.
✅ Delivers ultra-stable 3D data with near total immunity to ambient light levels.
Customer Stories
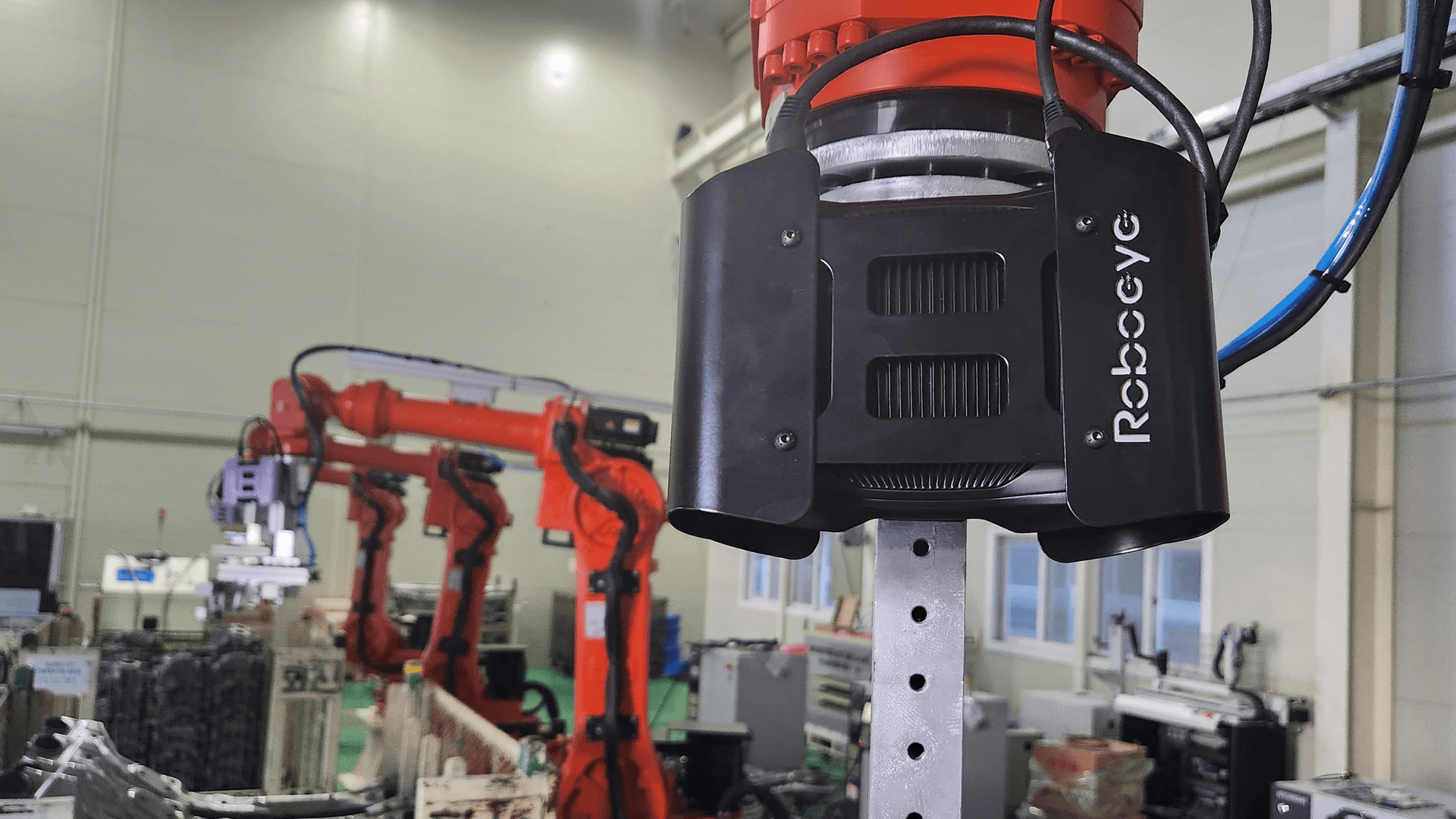
ING Robotics' all-in-one 3D vision solution for manufacturing
-2-2.webp?width=1144&height=640&name=Untitled%20(1144%20%C3%97%20614px)-2-2.webp)
Innodura's complex parts hanging solution for assembly lines
Hanging parts for processing is a task that has been primarily carried out manually, and automating it has proven to be a real challenge.
-1.webp?width=1920&height=1080&name=Scenario%20Automated%20Assembly%20with%20Zivid%20Two%203D%20camera%20-%20White%20Goods%20(1)-1.webp)
Plaif's appliance manufacturing solution
Plaif has leveraged advances in AI and 3D machine vision to bring a high-reliability solution in appliance manufacturing.