What is parcel induction?
AWL's Robotic Singulator (ROSI) is powered by Fizyr's software and Zivid's 3D camera
Before a parcel can be shipped from a logistics or sorting facility to its destination, it must be loaded, sorted and scanned in order to route the parcel to its destination. This process is called parcel induction and involves picking and singulation of parcels from a pile so that each parcel can be identified. Robot arms are being used to pick these parcels up and place them on a conveyor or robotic drive unit for downstream processing.
3D vision in parcel induction
Parcel segmentation and recognition
Using perception with 2D and 3D cameras, the robot searches a pile of parcels and attempts to segment each parcel from one another.
Locate and evaluate the robot's pick point
The robot attempts to estimate which of the detected parcels are best suited to be picked up, and where to grasp it. This is called pose estimation.
Repeat rapidly and reliably
While the robot is placing the parcel and returning back to the pile, the vision system selects the next parcel so the robot can proceed to pick it up without having to wait.
Why use a Zivid camera?
Design simpler and better robots
Perform segmentation, pose estimation, and collision checks with just one camera. Eliminate the need for additional illumination and other 2D cameras, simplify your robot cell, reduce costs, and deploy faster with less assembly and setup - all without sacrificing reliability or performance.
Zivid cameras combine the power of high-quality 2D and 3D cameras into a single device. Maximize your robot's performance with fast captures and flexible options for adapting resolution and parallelization to your needs.
Fewer multi-picks and robot-induced mistakes
Sharp, complete, consistent, and correct color and depth data ensure the robot’s ability to identify, target, and extract every item with a higher chance of success.
Zivid cameras work with any parcel - black, white, or glossy - under varying ambient light. Factory calibration and ambient light suppression technology ensure that both the 2D image and 3D point cloud remain stable, allowing your robot to operate more reliably.
2D + 3D in less than 50 ms
Parcel induction robots don’t have time to wait if they are to perform thousands of picks per hour. The next picking instruction needs to be ready before the robot finishes its previous task. Therefore, the 2D and 3D data must be captured extremely fast.
Zivid 3D cameras can capture and return 2D color images and point clouds of parcels in less than 50 ms. This ensures that your robot can pick at maximum speed without waiting for the camera.
Other 3D vision solutions
❌ The vision system limits the robot’s cycle time.
❌ It causes the robot to double-pick parcels.
❌ It struggles to accurately process black poly mailers and bubble wrap.
❌ It lacks industrial robustness and is sensitive to ambient light conditions.
With Zivid 3D camera
✅ No impact on robot cycle time, ensuring seamless operation.
✅ Captures most packages in just 50 ms and all packages within 150 ms.
✅ Eliminates double picks with highly reliable segmentation, powered by ultra-crisp and stable 2D imaging.
✅ Provides complete visibility of every item, delivering clean and accurate point clouds—even for challenging packages like black poly mailers.
✅ Delivers ultra-stable output with near-total immunity to ambient light.
Customer Stories
.png?width=1920&height=1080&name=item%20picking%20by%20Fizyr%20(1).png)
Handling unknown objects in logistics
Fizyr detection and picking software, together with Zivid 3D cameras are solving biggest logistics challenges.
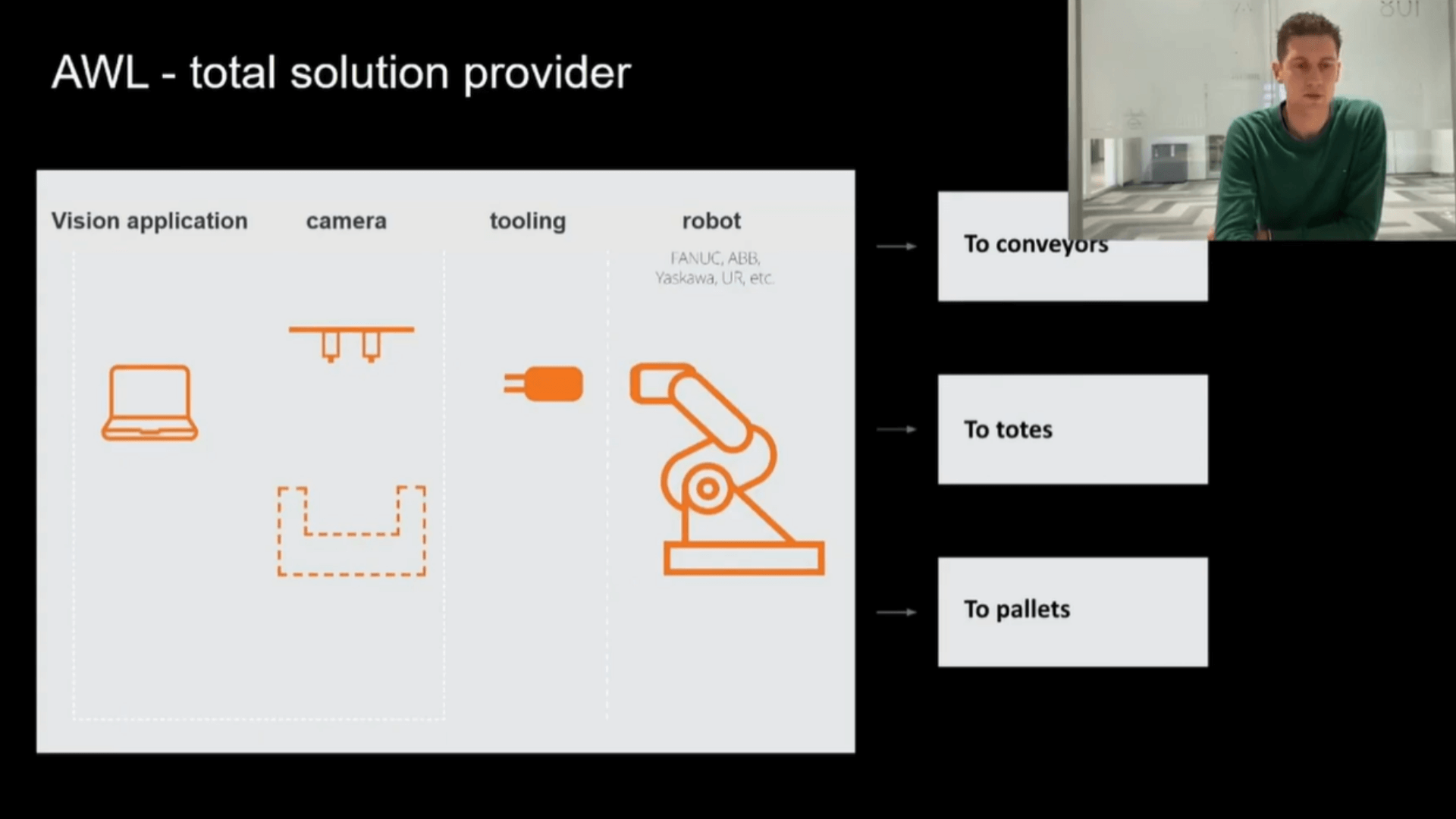
Changing the Game of Parcel Sorting with 3D Vision
By collaborating with partners, we achieved the world's first successful sorting inductor in the logistics market.
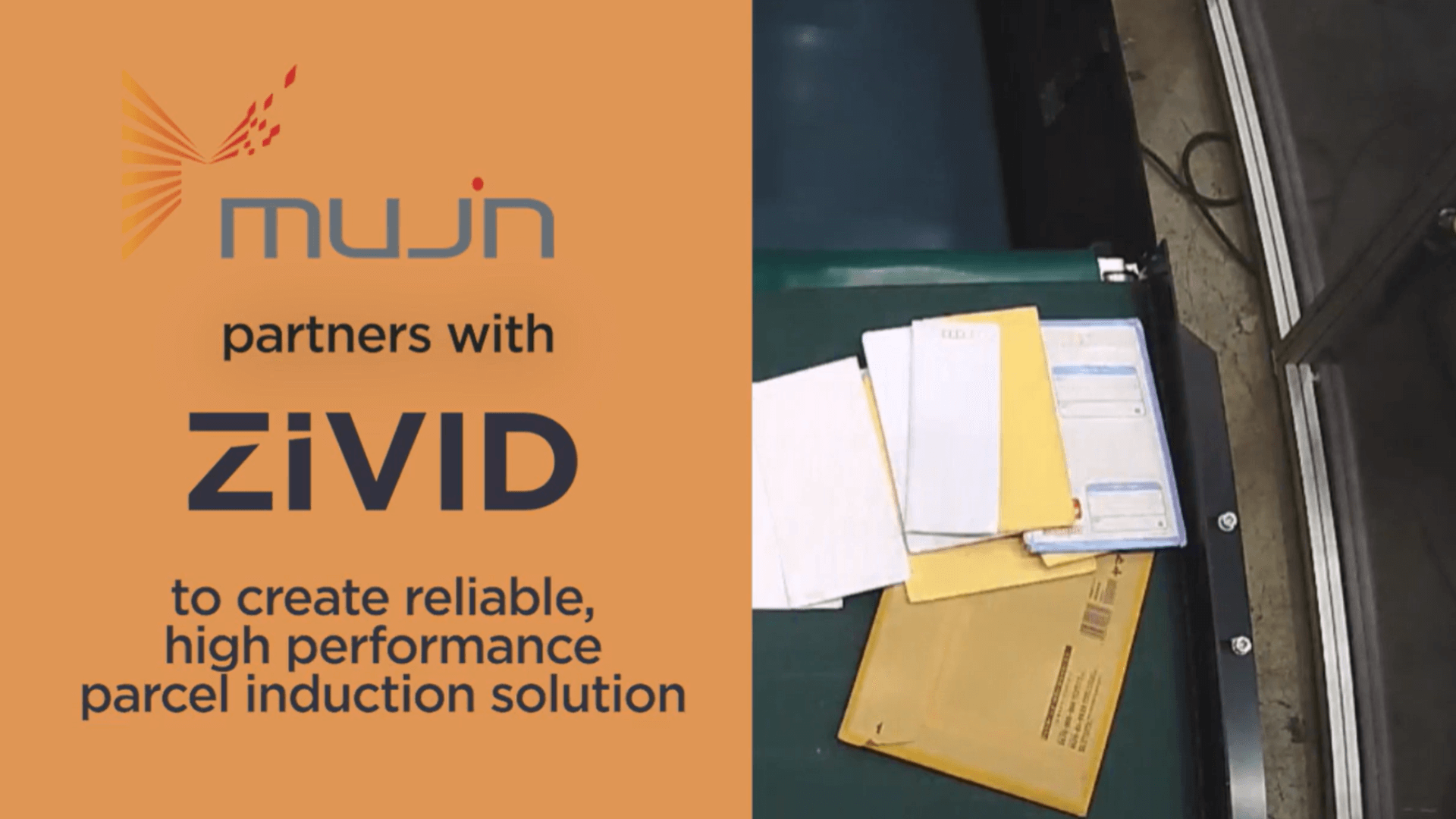
Parcel induction at high-speed
"Mujin managed to go from 700 to up to 1200 picks/h by switching to Zivid's newest model, the Zivid 2+ LR110" says Floris Gaisser, Computer Vision Sub-team lead at Mujin.
Watch the video →